The study of machine vision began with the pattern recognition of two-dimensional images in the 1950s. It was actually designed to replace human eyes in the detection and identification work, which can greatly improve the detection efficiency and reduce the detection results caused by human eye fatigue. The inconsistency. Since the development of machine vision inspection, many aspects have been developed to accomplish tasks that are difficult for human eyes to complete, and infrared, ultraviolet, and X-ray detection technologies are used to detect things that cannot be detected by human vision. However, the difficulty in the design of machine vision system lies in how to ensure its reliability and stability. Whether it is from light sources, cameras or other hardware or image processing software, it has an important influence on the stability of machine vision.
Imaging System Introduction and Instability Factors
The imaging system is mainly composed of a camera (CCD/CMOS), a lens, and a light source, and is the basis of visual inspection. The imaging system is designed to obtain qualified original images, and a good imaging system is required to ensure the stability of image quality during system operation. Stable image capture is the basic guarantee of visual inspection stability.
1, the impact of industrial cameras on imaging stability
For vision system designers, the choice of industrial camera mainly considers its sensor type, resolution and frame rate, in which the sensor is divided into CCD and CMOS. The integration of CMOS image sensor is high, and the distance between components and circuits is very short. The interference is severe, and the imaging noise is high. The CCD sensor camera has high sensitivity, low noise, and fast response compared to the CMOS camera. In terms of stability, the CCD camera is also resistant to shock and vibration. Generally speaking, the CCD camera is relatively strong. The sensor camera is superior to the CCD camera in image quality and stability.
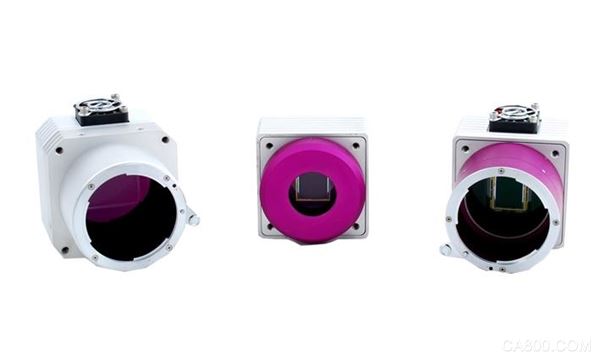
Another important factor affecting the imaging quality of the camera is the lens of the camera. In addition to the parameters such as focal length, depth of field, and aperture required for the lens according to the specific working conditions, an important factor that affects the accuracy of the system detection is the geometric distortion error of the image. The inherent perspective distortion of optical lenses is influenced by the manufacturing process and cannot be eliminated. It can only be compensated. Although many industrial cameras now compensate for the lens distortion caused by various methods, geometric distortion will still be detected in the field of high-precision detection. Accuracy affects.
2. Effect of light source on imaging stability
The light source has the effect of magnifying the characteristics and defects of the image, weakening the chaos and the background, and directly affecting the quality of the input data. Because there is no universal lighting device, the design of the light source has always been a difficult point of the machine vision system, and usually not only for each specific application. Examples to select the type of light source, but also according to the specific environment of the light source installation, the light source illumination mode discretion, in order to achieve the best results. There are differences in the stability of different types of light sources. Common visible light sources include LED light sources, halogen lamps, fluorescent lamps, and sodium light lamps. The biggest drawback of visible light is the inability to continuously output stable light energy, such as fluorescent lamps, in the first 100 used. Within a few hours, the light energy will drop by about 15%. With the increase of the use time, the light output will continue to decrease. In addition to visible light, under the scene of high detection tasks, invisible light such as X-rays and ultrasonic waves is often used as a light source, which can continuously and stably output light energy, but is not conducive to the operation of the detection system and is expensive. The inhomogeneity of the light source also affects the image quality, and the difference in the light intensity in different directions also causes noise. The stability and life of the LED light source in the visible light are better than that of the halogen lamp, fluorescent lamp, etc., the response time is short, the color can be freely selected, the operating cost is also low, and it has been widely used. Illumination of light sources can be divided into back-illumination, forward-direction illumination, structured-light illumination, and stroboscopic illumination. The main point of design is to emphasize the characteristics of the image.
3, software stability
The influence of software stability on machine vision is beyond doubt. The vision system will eventually use software to perform targeted filtering on the computer for image filtering, edge detection and edge extraction and a series of image processing, different image processing and analysis methods, and Different detection methods and calculation formulas will bring different errors. The quality of the algorithm determines the accuracy of the measurement.
4, environmental factors
The measurement environment in which the vision system works includes temperature, light, power supply changes, dust, humidity, and electromagnetic interference. A good environment is the guarantee for the normal operation of the vision system. The external light affects the total intensity of the light irradiated on the measured object, and increases the noise of the image data output. The change of the power supply voltage also causes the light source to be unstable and generate noise that changes with time. Temperature changes will also affect the performance of the camera. The camera will mark the normal operating temperature range when it is shipped from the factory. Overheating or undercooling will affect the camera's normal operation. Electromagnetic interference is an unavoidable interference factor on industrial inspection sites. It affects the weak circuits of industrial camera circuits and data signal transmission circuits. Qualified visual products are subjected to strict anti-jamming tests at the factory, greatly reducing External electromagnetic interference on the hardware circuit.
5, mechanical structure positioning effect
In addition to the imaging system hardware, the relative positional relationship between the camera and the object also affects the stability of the image quality. For example, if the camera or the mechanical support structure of the workpiece is shaken, it will affect the detection accuracy, and this is also a difficult to troubleshoot. problem. Detection of the workpiece under dynamic conditions requires consideration of the effect of motion blur on image accuracy (blurred pixels = object motion speed * camera exposure time). In addition, between the CCD camera and the tested part, the optical axis of the camera lens should be perpendicular to the plane where the part is located under rational conditions. However, in actual use, the optical axis and the measured plane cannot be guaranteed due to installation errors or camera and workpiece manufacturing errors. It is completely vertical and there is a certain angle deviation, which also affects the measurement accuracy.
The above are some of the factors that may affect the detection effect of machine vision systems as summarized by Shenzhen Huazhou Measurement & Control Technology Co., Ltd. In fact, choosing a good machine vision inspection system requires the cooperation of all parts and components. On the model, we need to select the most suitable part. Huazhou Measurement and Control Machine Vision provides you with the most comprehensive and cost-effective machine vision selection program. For details, please contact Hua Zhou's monitoring and control staff.
Http://
Parallel & Synchronization Panel
Parallel system for multi gensets and Mains Grid
. Parallel panel
. Synchronizaiton system
. Load sharing system
. Power management system
. ACB breaker: ABB, CHINT, DELIXI,
. Multi gensets parallel
. Synchronized to Grid
. Group parallel or couple
. Controller: Deepsea, ComAp, Deif, SmartGen
Parallel Panel,Genset Parallel,Synchronization Panel,Synchronization System
Guangdong Superwatt Power Equipment Co., Ltd , https://www.swtgenset.com