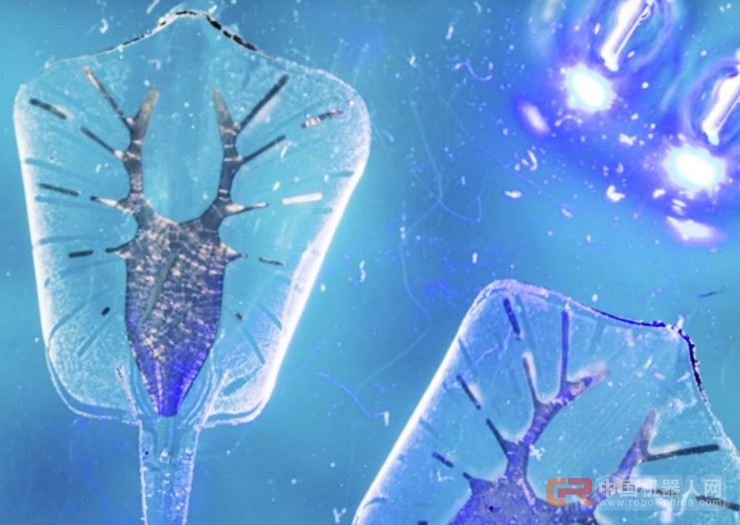
When you hear robots, what most people have in mind is a bunch of metal-plastic components made of hardware—they are usually hardware robots assembled from various nut bolts. At the moment, the robot is leaving the laboratory and walking into everyday life of the people to take on various tasks. For people dealing with robots, such hardware design poses security risks. For example, when an industrial robot "carelessly encounters" a human worker, the consequences are not a joke - it is often bruised and bruised. How to deal with the security risks of hardware robots? Engineers all over the world are more and more inclined to make robots softer and more submissive—no longer a hard machine, but rather closer to a “light and easy-to-tuck†critter. For a conventional drive such as a motor, this means using an artificial "air muscle" or adding a spring structure to the drive train.
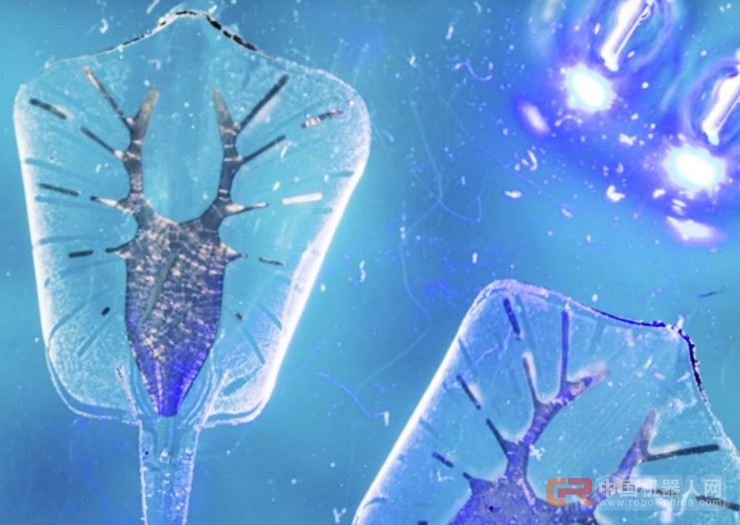
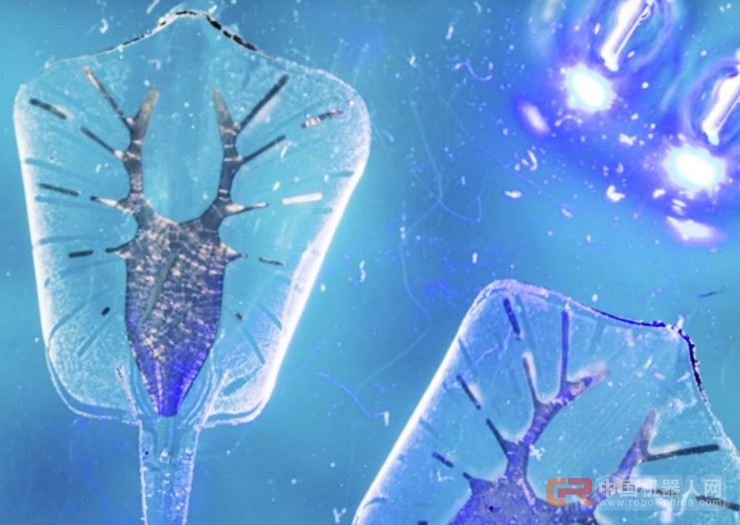
Festo, Germany: Conceptual Diagram of an Air Muscle Robot Another example is the Whegs robot of Case Western Reserve University. There is a spring device between the motor and the wheel. When hitting someone, the spring can absorb some of the energy and reduce personal injury. See below:
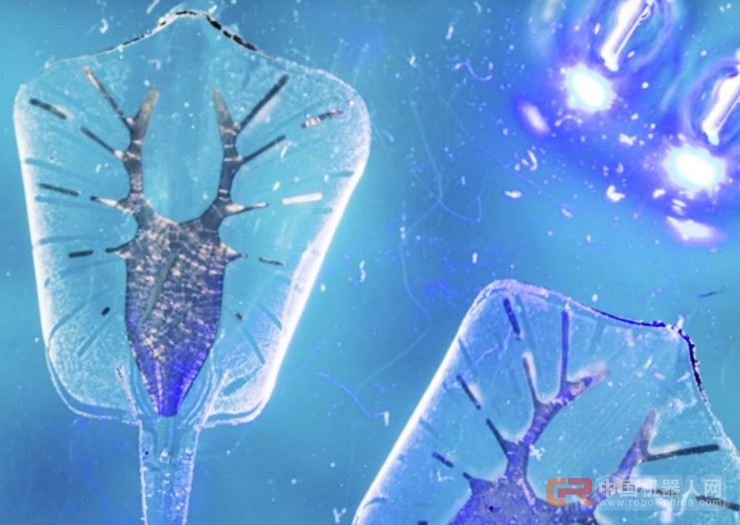
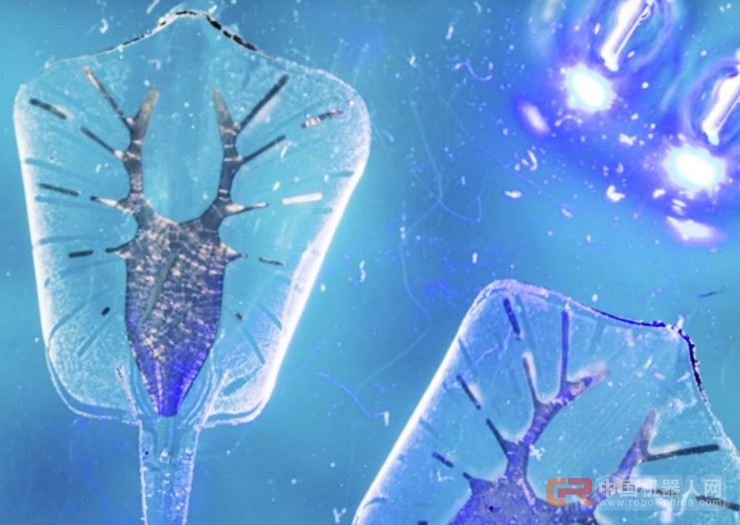
The Roomba sweeping robot is another example. Its bumper is spring-loaded and does not damage what it hits (similar to a car's fender).
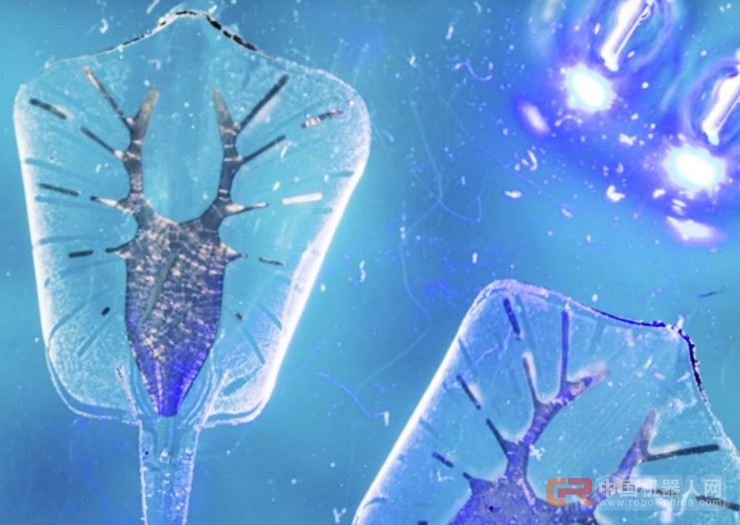
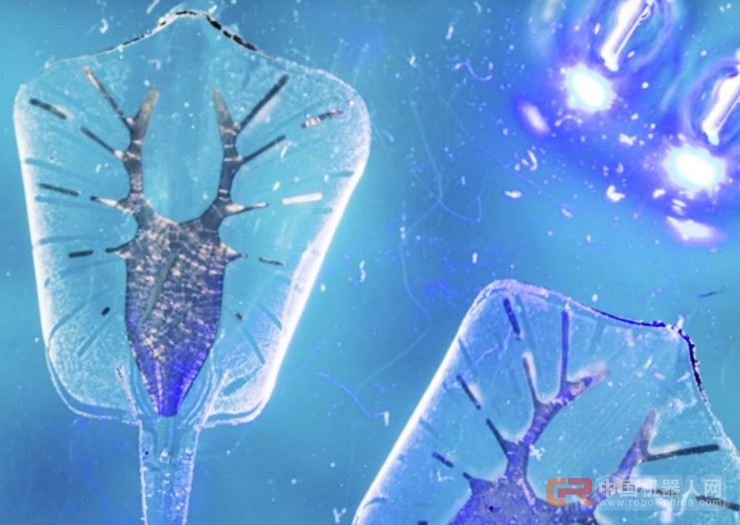
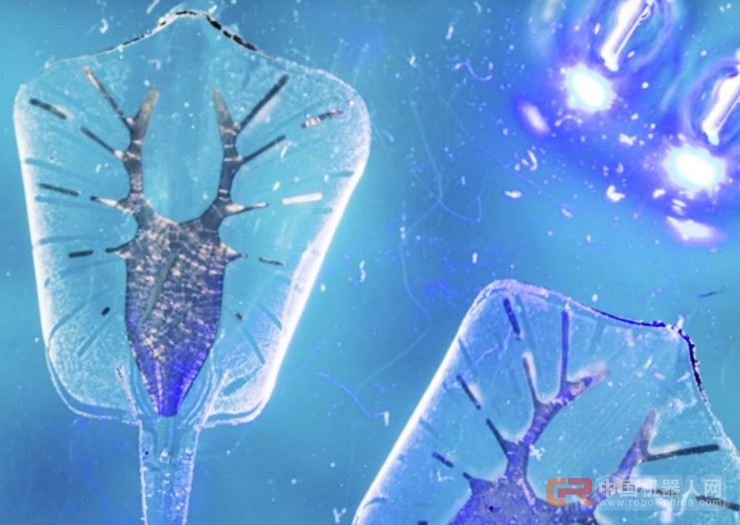
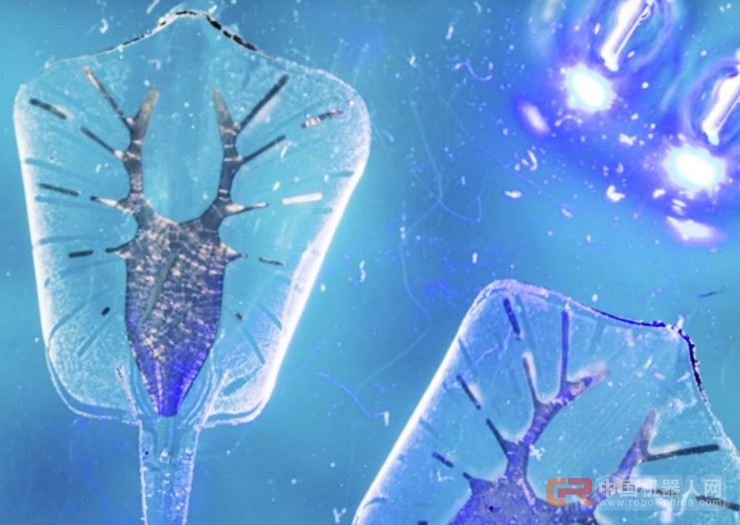
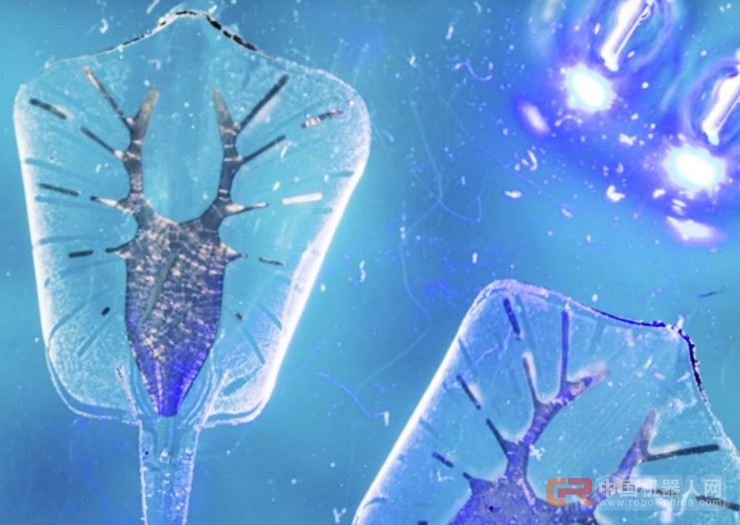
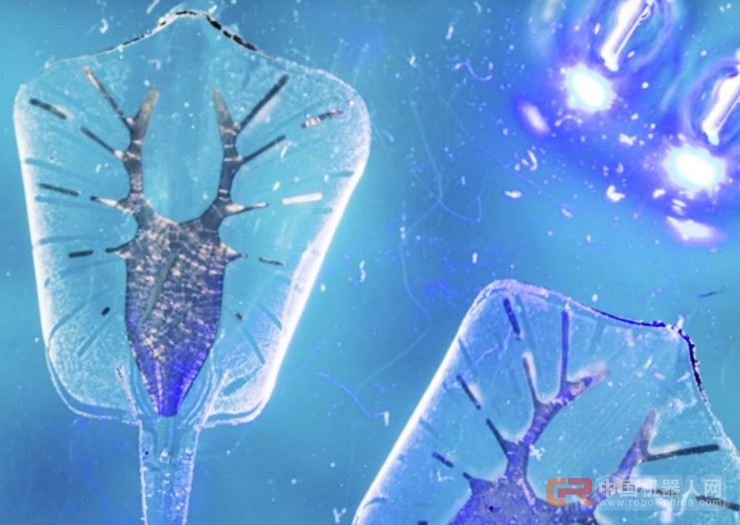
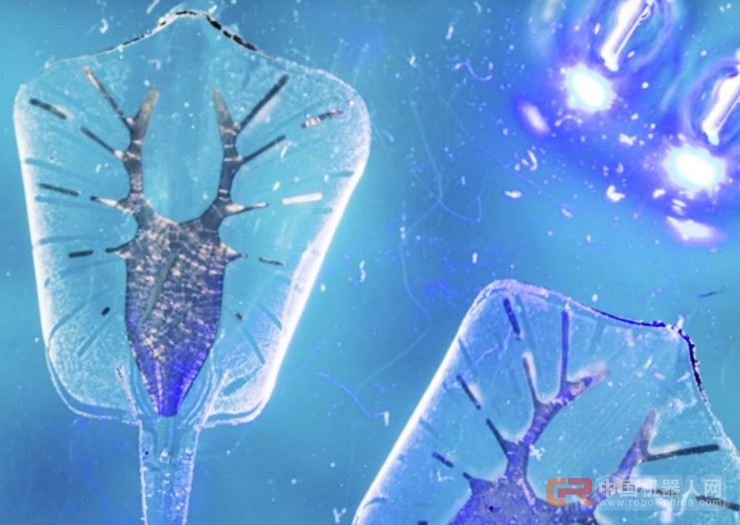
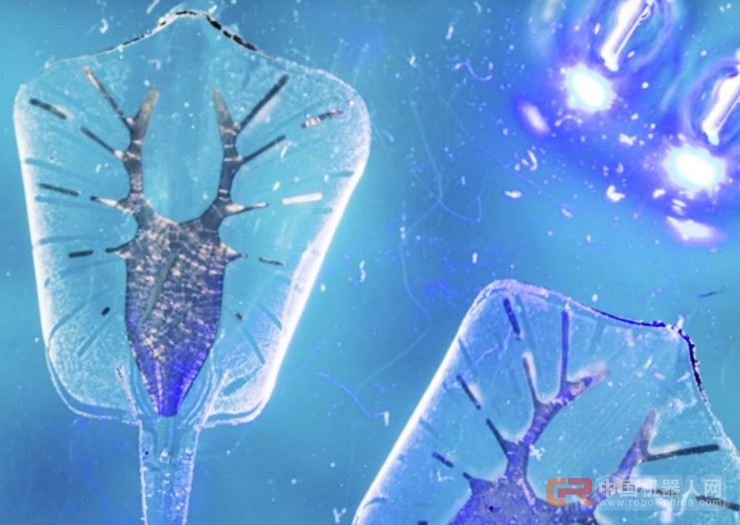
Bio-robots using some sea snails Challenges and perspectives Another big challenge for bio-robots is that no airborne control system (mounted on robots) has been developed yet. Engineers can only control them through external electric fields or light. In order to develop a fully autonomous biosynthetic robot, we need a controller that can directly communicate with robotic muscle tissue and provide sensor input. The seemingly straightforward solution (and probably the most difficult one) is the use of neurons composed of neurons or neuron clusters as biological controllers. This is another reason why researchers are so concerned about sea snails: it has been used as a model system by neurobiological research for many years. Its relationship between the nervous system and muscle has been studied more thoroughly. This opens the door to using its neurons as biological controllers. In the future, researchers hope to use the biological controller to tell the robot how to move and help it deal with various tasks, such as finding toxic substances and following light. The field of synthetic biology is in its infancy, but researchers have already envisioned many applications for it. For example, a group of mini-robots using sea snails can be created and then a large group can be released into reservoirs or seawater to search for leaking pipes or toxic substances. Since these robots are made of biological tissue, if they are broken or eaten by marine fish, they will not have a great impact on the environment. In the future, biological robots manufactured using human cells can be applied to the medical field. As far as Leifeng.net knows, they can carry out targeted drug delivery, handle thrombosis, or become a controlled, adjustable stent. These mini-robots strengthen weakened blood vessels to prevent aneurysms. Due to the use of biological media, rather than polymers, they can be readjusted and become part of the patient's body over time. In addition, advances in biological tissue engineering (such as the development of artificial blood circulation systems) are likely to open a new door: large-scale biological robots that act on muscles.
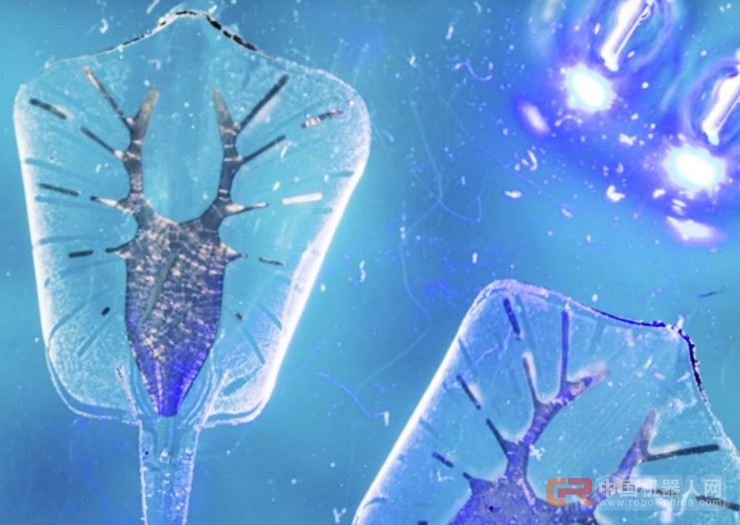
gree , https://www.greegroups.com